CHAPTER 1 GENERAL INFORMATIONEQUIPMENT, ACCESSORIES AND DOCUMENTS SUPPLIED.Table 1-1 Characteristics of the IABTable 1-2. Equipment, Accessories, and Documents Supplied with the IABCHAPTER 2 INITIAL ASSEMBLY AND INSPECTION Figure 2-1. Rigid Flooring System.Positioning Intercommunicating Valves.Figure 2-3. Intercommunicating Valve.INFLATION OF AIR CHAMBERS.Figure 2-4. location of Isolator Clamps.Inflate Keel.Figure 2-5. Intercommunication valve base nut.Figure 2-6. Tightening Keel Valve Base Nut.Figure 2-8. Lower Buoyancy Tube Inflation Fitting Base Nut.Figure 2-10. Stowage Location for Paddles.Figure 2-11. Floor Runner and Straps.CHAPTER 3 FUNCTIONAL DESCRIPTIONFigure 3-2. Main Buoyancy Tube (MBT)Intercommunicating Valves.Figure 3-4. Intercommunicating Valve Components.Figure 3-5. Intercommunicating Valve Positions and Functions.Figure 3-6. Bow Stowage Pouch.Figure 3-7. Foot Pump and Air Hose.Figure 3-9. Stowage Sheaths and Paddles.Figure 3-10 Chafe ProtectionForward and Aft Towing Rings. Figure 3-11. Transom.Figure 3-13. Self-Bailers and Anti-Splash Triangles.Figure 3-14. Inflatable Keel (Flooring Removed)Figure 3-15. Clamp.Figure 3-16. Carrying Bag.Figure 3-17. Semi-Rigid Flooring System.Figure 3-18. Components of the CO2 System.CHAPTER 4 OPERATIONTrim and Balance.Outboard Engine Adjustment.Section II. OPERATIONCO2 Overpressure Valves. Outboard Engine.Securing Equipment.Figure 4-5. Lower Grab Lines.Righting the F530 IAB.Figure 4-9. Correct towing procedure, Crossing of Towing Harness Lines.Lifting.Figure 4-10. F530 IAB Lifting Sling.Trailering.CHAPTER 5Section III. ORGANIZATIONAL AND INTERMEDIATE MAINTENANCEORGANIZATIONAL MAINTENANCE.Buoyancy Tube Pressure Check.Table 5-1. Scheduled Maintenance Action Index.Keel Pressure Check.Keel Pressure Check. - ContinuedTIGHTNESS CHECK OF OUTBOARD ENGINE MOUNTING CLAMP SCREWS.'Unknown' by warda.s.sheikh - Page 62 of 276Figure 5-1. Craft Resting on the Cone Ends, Flooring Removed.MONTHLY CLEANING OF CRAFT WITH FLOORING REMOVED.INTERCOMMUNICATING VALVE CLEANING AND LUBRICATINGFigure 5-2. Required Tools and Materials.Intercommunicating Valve Cleaning Procedures.Figure 5-3. Spanner Used to Tighten Base Nut Clockwise (to be done while buoyancy tube is inflated to operating pressure).Figure 5-4. Intercommunicating Valve Components.Intercommunicating Valve Cleaning Procedures. - ContinuedFigure 5-5. Cleaning Male Portion of Intercommunicating Valve.Figure 5-6. Removing Flat Ring-shaped Neoprene Valve Insert Gasket from Metal Valve Insert.Intercommunicating Valve Cleaning Procedures. - ContinuedFigure 5-9. Pulling Diaphragm Stem into Seated Position.Figure 5-10. Valve Spring Washer and Spring Slipped over Screwdriver before Installing in Valve.Figure 5-11. Checking Tightness of Keel Valve Base Nut (to be done while keel is inflated at 220/240 mb [3.2/3.5 psi])Figure 5-12. Keel Valve Metal Cap and Metal Valve InsertFigure 5-13. Keel Valve Parts to be serviced.Figure 5-15. Inspecting Ring-shaped Flat Neoprene Valve Insert Gasket for Cuts and Cracks.Keel Valve Cleaning Procedures.Figure 5-17. Pulling Stem of Diaphragm into Seated Position.PAINTING TRANSOM, THRUSTBOARD, AND PADDLESPaint Procedure.CO2 ONE-WAY VALVE DIFFUSER INSPECTIONSCHEDULED PERFORMANCE TEST.Figure 5-22. Keel Pressure Test.Figure 5-23. Keel Pressure Test.PRESSURE RETENTION TESTS.INTERMEDIATE MAINTENANCE.Scheduled Daily During Periods of Craft Use.Section IV. CARE AND PREPARATION FOR STORAGE/SHIPMENTCARE AND PREPARATION FOR STORAGE/SHIPMENTCHAPTER 6 TROUBLESHOOTINGTable 6-1. Fault Isolation Procedures.Table 6-1. Fault Isolation Procedures - ContinuedTable 6-1. Fault Isolation Procedures - ContinuedAIR LEAK TEST.Figure 6-1. Brushing Soap and Water Solutions on Craft.Figure 6-2. Possible Valve Leak Location.WATER LEAK TEST.Procedures for the Water Leak TestProcedures for the Water Leak Test - ContinuedCHAPTER 7 CORRECTIVE MAINTENANCESection III. ORGINAZATIONAL LEVEL CORRECTIVE MAINTENANCEPatching Fabric with the Onboard Repair Kit.VALVE LEAKS.Figure 7-1. Location of Valve Leaks Caused by Valves Not Receiving Scheduled Maintenance.Figure 7-3. Location of Valve Leaks Caused by Loose Base Nut or Loose or Scarred Metal Compression Gasket. Figure 7-5. Location of Valve Leaks Caused by Valve Cap Gasket, Valve Cap Threads, or Valve Insert Upper Threads.KEEL VALVE LEAKSCO2 OVERPRESSURE VALVE LEAKS.Figure 7-6. Foot Pump Components.REPLACING BOWLINE AND GRAB LINE.Figure 7-7. Eye Splice for Bow Line and Grab Line Ends.Section IV. INTERMEDIATE LEVEL CORRECTIVE MAINTENANCEFigure 7-10. Intercommunicating Valve Extractor Tool.Figure 7-11. Tapping to Loosen the Male Portion of a Stuck Intercommunicating Valve.Regrind the Mating Surfaces of the Intercommunicating Valve.Regrind the Mating Surfaces of the Intercommunicating Valve. - ContinuedFigure 7-12. Using a Dremmel Tool to regrind Intercommunicating Valve.Figure 7-13. Tracing Lines with a Grease Pencil to verify that the Intercommunicating Valve is Properly Reground.Remove and Replace Intercommunicating Valve Large Neoprene Washer.Figure 7-14. Removing the Intercommunicating Valve Base Nut.Remove and Replace Intercommunicating Valve.Remove and Replace Intercommunicating Valve. - ContinuedFigure 7-15. Location of the Incision to Replace an Intercommunicating Valve.Figure 7-16. Intercommunicating Valve Components.Remove and Replace Intercommunicating Valve. - ContinuedFigure 7-17. Keel Valve Components.Figure 7-18. Loosening the Keel Valve Base Nut.Remove and Replace the Keel Valve.Figure 7-20. Loosening the Keel Valve Base Nut.Remove and Replace the Keel Valve. - ContinuedFigure 7-21. Loosening the CO2 Inlet Valve Base Nut.Remove and Replace the CO2 Inlet Valve Base.Figure 7-22. CO2 Inlet Valve Components.Figure 7-23. Loosening the CO2 Inlet Valve Base NutRemove and Replace the CO2 Overpressure Valve and Valve Base.Remove and Replace the CO2 Overpressure Valve and Valve Base. - ContinuedFigure 7-25. CO2 Overpressure Valve Components.Figure 7-27. Removing Part of the Internal CO2 Overpressure Neoprene Valve Insert Base and Installing an External Neoprene Valve Insert Base.Figure 7-28. External Neoprene Valve Base and Ring shaped Patch to Repair CO2 Overpressure Valve Base.Remove and Replace the Lower Buoyancy Tube Inflation Hose Barbs.Figure 7-29. Lower Buoyancy Tube Inflation Hose Fitting Components.REMOVING FIELD REPAIR PATCHES APPLYING PERMANENT PATCHES.RESTORING AIR TIGHTNESS TO AN OLDER CRAFT.Figure 7-30. Marking Template for Tube Seam Bandages.Figure 7-31. Marking Area to Receive a Seam Bandage.Latexing Buoyancy Tubes.Latexing ProcedureLatexing Procedure - ContinuedREPAIRING/REPLACING INFLATABLE KEEL. Keel Velcro Fastener Modification.REPAIRING DAMAGED HULL BOTTOM.Figure 7-32. Velcro Modification to Inflatable Keel.CORRECTING HULL BOTTOM TENSION.Figure 7-36. Ungluing the Self-Bailer Circular Patches after Application of Heat.General Rubbing Stake Replacement Procedure.MAINTENANCE ALLOCATION CHART (MAC)Explanation of Columns in the MAC, Section II.Explanation of Columns in Tool and Test Equipment Requirements, Section III.Explanation of Columns in Remarks, Section IV.MAINTENANCE ALLOCATION CHARTMAINTENANCE ALLOCATION CHART - ContinuedMAINTENANCE ALLOCATION CHART - ContinuedComponents of End Item (COEI) and Basic Issue Items (BII) Lists.Section II, Components of End Item.Section III, Basic Issue Items.Hose BarbOverpressure ValveKeel ValveIntercommunicating ValveIAB Overall ViewIAB Overall View - ContinuedIAB FUEL BLADDER 6 GALLONFloorboard ViewMiscellaneous EquipmentMiscellaneous Equipment - ContinuedSpecial ToolsCO2 DiffuserTransom ViewBASIC ISSUE ITEMSEXPENDABLE AND DURABLE ITEMS LISTSECTION II EXPENDABLE/DURABLE SUPPLIES AND MATERIALS LISTSECTION II EXPENDABLE/DURABLE SUPPLIES AND MATERIALS LIST - ContinuedREPAIR PARTS FOR ZODIAC F530 IABHose BarbOverpressure ValveHR/OP VALVEKEEL VALVEKeel ValveIntercommunicating ValveINTERCOMMUNICATING VALVES (I/C)OVERALL VIEWOverall ViewOverall View - ContinuedFUEL BLADDER 6 GALLONFUEL BLADDER - ContinuedFLOORBOARDFloorboard ViewMiscellaneous EquipmentMISCELLANEOUS EQUIPMENT - ContinuedMISCELLANEOUS EQUIPMENT - ContinuedMISCELLANEOUS EQUIPMENT - ContinuedSpecial ToolsSpecial Tools - ContinuedCO2 DIFFUSERCO2 DiffuserTransom ViewTRANSOM ASSEMBLYRECOMMENDED REPAIR FACILITIES, TOOLS, AND EQUIPMENTRECOMMENDED CONSUMABLE ITEMS.Table E-1. Recommended Tools for the F530 IAB Repair Facility.Table E-1. Recommended Tools for the F530 IAB Repair Facility - ContinuedTable E-1. Recommended Tools for the F530 IAB Repair Facility - ContinuedTable E-1. Recommended Consumable Items for the F530 IAB Repair Facility.Table E-1. Recommended Consumable Items for the F530 IAB Repair Facility. - ContinuedSPECIAL SHOP PRACTICES FOR F530 IAB FABRIC REPAIRFigure F-1. Composition of Coated Fabrics.Figure F-2. Thread Direction and Stretch Characteristics of Fabric.Figure F-4. Determining the Bias Angle and Marking Fabric before Patches are Cut.Figure F-6. Using a Dremmel Tool to Scuff the Area Where a Patch will be Glued.SCUFFING FABRIC.GLUING FABRIC.Mixing Glue.Application of Solvent.Figure F-7. Applying Solvent to Prepare Material for Gluing.Figure F-8. Tape Applied Around Area Not to Receive Glue.Figure F-9. Applying Glue to the Area to be Patched.Joining the Surfaces.Figure F-11. Smoothing the Patch with a Solvent Dampened Towel.Figure F-12. Rubbing Patch Down with Boning Knife.Table F-1. Gluing Schedule.Figure F-13. Using a Heat Gun to Soften the Glue Bond during Ungluing.PATCHING TECHNIQUES.Inner Patches. Figure F-14. Tracing the Patch onto the Craft with a Silver Pen.Tear in Buoyancy Tube at a Baffle.Hull IdentificationZODIAC LIMITED TECHNICAL INSPECTION FORMZODIAC LIMITED TECHNICAL INSPECTION FORM - ContinuedINTERCHANGEABILITY OF PARTS BETWEEN THE F470 AND F530 IABINTERCHANGEABILITY OF PARTS BETWEEN THE F470 AND F530 IAB - ContinuedINTERCHANGEABILITY OF PARTS BETWEEN THE F470 AND F530 IAB - ContinuedINTERCHANGEABILITY OF PARTS BETWEEN THE F470 AND F530 IAB - ContinuedINTERCHANGEABILITY OF PARTS BETWEEN THE F470 AND F530 IAB - Continued
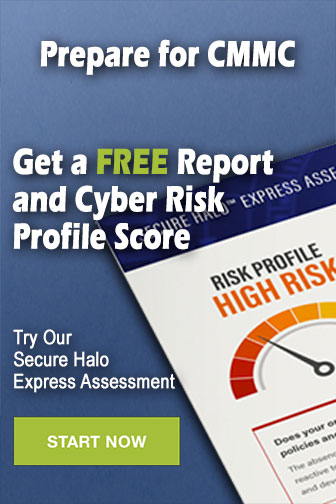